今后,IoT(物联网)设备普及伴随的课题——半导体封装的多品种、少量、变量生产将得到解决。有一家企业已经开发出了这样的芯片装配技术。那就是 2009年成立、总部设在日本新潟县妙高市的CONNECTEC JAPAN。现在主要从事半导体后工序的受托开发和制造。
CONNECTEC JAPAN自主开发的装配技术名叫“MONSTER PAC”。该公司代表董事平田胜则介绍说,“不仅可以多品种少量生产,还能一举解决因low-k化而脆化的半导体芯片的安装、在不耐高温的基板上的安装、 MEMS(微电子机械系统)倒装芯片安装等目前半导体后工序存在的课题”。
利用凹版印刷实现
MONSTER PAC的关键,是在基板侧设置用来接合芯片和基板的微凸点。微凸点使用凹版印刷技术形成(图1),墨水采用银纳米膏。形成凸点后在其上方涂布非导电性树脂。
图1:在基板上印刷凸点
在基板上印刷凸点的方式适用于多种材料的基板。非导电性树脂起到维持凸点的形状、保护芯片与基板的界面的作用。(供图和摄影:CONNECTEC JAPAN) (点击放大)
平田称,因为是印刷方式,所以“可以在任何基板材料上形成布线,实现多品种少量生产”。而且,这种方式不仅可以缩短形成微凸点的时间,还可以大幅简化装置。
原来的方法是在芯片上形成微凸点,要对晶圆进行电镀处理。这必须经过形成光刻胶膜、电镀处理、剥离光刻胶膜等步骤才能实现,而且装置的体积都较大。采用印刷方式可以省去这些处理。
还技术还能用于MEMS倒装芯片的装配。MEMS的芯片上有沟槽等结构体,芯片的电极不能进行电镀处理。但MONSTER PAC技术无需对芯片进行加工,因此可以用于倒装芯片的装配。
在低温和低载荷下进行接合
与以往技术相比,MONSTER PAC的芯片装配操作也有所简化。只要在印刷了微凸点的基板上放置芯片,施加170℃、0.12g/凸点的载荷,就能完成接合。而采用在芯片上形成微凸点的方法时,需要2.4g/凸点的接合载荷,并加热到260℃。2.4g/凸点的载荷看上去很小,但几千个微凸点相加,需要施加相当大的力。在强大的作用力下,芯片有时会发生破损。
这种问题*近尤为突出。这是因为,为了减少微细化造成的布线间电容量的影响,用来支撑布线的层间绝缘膜材料倾向于选择介电常数低的low-k材料。实现 low-k的一般方法是采用多孔质材料,使介电常数接近空气。因为内部开有很多小孔,所以材料强度会减弱。而MONSTER PAC无需顾忌此类问题,不受任何影响。
除此之外,MONSTER PAC还具有一种安装设备适用于陶瓷、有机材料、薄膜材料等多种基板材料的特点。极端地说,可以在每道工序安装不同的基板。而使用传统方式时,必须为不同的基板材料准备不同的设备。这种不挑剔材料的特点,非常适合少量多品种生产。
有意对外销售技术
CONNECTEC JAPAN正在开发以10μm为间隔的凸点布线技术,实用化已有了眉目(图2)。在晶圆上电镀形成凸点的通常方式长期受到40μm的制约。原因是接合需要加热,会使有机材料大幅膨胀。而CONNECTEC正在开发的技术可以在130℃的温度下接合,膨胀量小,因此间隔可以缩小到10μm。间隔缩小到 10μm后,封装的面积可以缩小75%。“到2017年,使用10μm间隔技术的产品可以投入量产”(平田)。
图2:10μm布线显现眉目
通过改进印刷技术和和膏状油墨,实现了绘制10μm布线、130℃接合。具体方式是,使用照射激光后硬化的墨水制造凸母模,再利用凸母模制作凹复制模,作为底版进行印刷。(图:CONNECTEC JAPAN) (点击放大)
MONSTER PAC目前只在CONNECTEC JAPAN的内部使用,今后计划广泛销售后工序生产设备。生产设备的目标是使模具制造、凸点印刷和布线、安装能够全部设置在一张长桌上(图3)。使用家用 100V电源驱动。平田心中的梦想是:“要在日本的土地上,孕育出众多以便利店那样小的面积,承接半导体封装工序的企业。”(记者:中道理)
图3:CONNECTEC JAPAN描绘的未来的后工序
利用长桌上的3台机械完成封装。
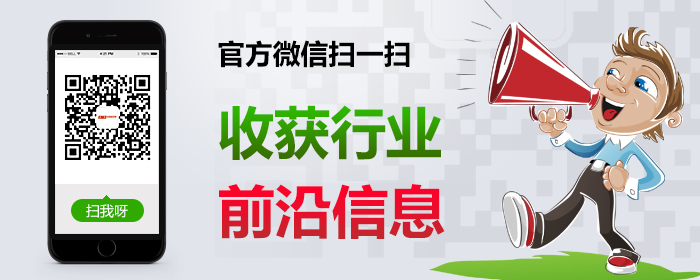
