本报记者 徐恒
在智能制造的大潮中,江苏省一大批重点骨干企业结合自身实际和行业特点,积极探索系统化智能制造,建成了一批智能车间,具备了智能工厂的雏形和潜质,天合光能有限公司(TSL,简称天合光能)就是其中的代表。
天合光能新闻发言人叶超向《中国电子报》记者坦言,太阳能光伏市场经过多次大浪淘沙,不仅行业内市场竞争异常激烈,行业外还要与其他能源同台竞争,因此,公司迫切希望通过技术改造和技术**降低生产成本,提高生产效率,推进智能车间建设显得水到渠成。“智能车间整体计划完成后,将有利于产品质量的提升和稳定,电池组件车间整体人力需求可以在原有的基础上减少20%以上,良率提升0.2%以上。”叶超说道。
智能车间折射
行业发展大趋势
天合光能智能车间项目投资55118万元,计划在电池车间导入自动化设备120台(套)。
近日,江苏省经信委对外公布了江苏省**批示范智能车间,共70个,天合光能光伏电池及组件智能生产车间在列。“罗马不是**建成的”,同样,天合光能智能车间也不是拍脑袋一下子就建成了。
据天合光能组件生产经理石鹤介绍,早在几年前,受到国内外复杂的经济环境影响,光伏行业跌入谷底,人力成本逐渐上升,很多企业陆续倒闭。天合光能高层深思熟虑,通过认真分析行业形势发展趋势,对比新技术应用成本与人力成本发展轨迹,认为自动化技术的成本下降趋势线和人力成本的上升趋势线将在2012年有个交叉点,于是决定于2012年开始**上马智能车间项目,提高车间自动化、智能化水平,降低人力成本,使公司在激烈的行业竞争中占据主导权。
据介绍,天合光能智能车间项目总投资55118万元,计划在电池车间导入前后清洗自动上下料、PECVD自动上下料、扩散自动插片机等行业内**的自动化设备共约120台(套)。组件车间导入串焊机40台,组件车间自动化流水线6条。通过新增和改造部分生产设备,达成生产线自动化改造和升级的目的,生产规模保持原有规模不变的同时,力求提高生产效率并降低生产成本。
“智能车间的实施成功,将形成具有自主知识产权的光伏产品研发和大规模批量化生产基地,对进一步推动区域产业结构调整起到积极的促进作用。同时,智能车间的实施,有助于天合光能更好地降低生产成本,简化生产流程,提高产品质量,向客户提供具有竞争力的产品,进一步保持天合光能在光伏行业的**地位。”叶超向记者坦言。
车间自动化程度
接近80%
通过智能车间改造,组件和电池车间自动化程度接近80%,提高了车间的生产效率。
“这里以前有很多工人,换工作服的地方人满为患,现在工人数量已大大减少,换工作服的空间也被挪为他用了。”记者顺着石鹤的手,来到天合光能M4车间,自动排串机、串焊机等机器设备正在有序运行,为数不多的工作人员只需负责机器操控和产品检验,与几年前的劳动密集型生产线大相径庭。“生产500兆瓦产品,2012年需要近800名工人,智能车间项目实施后,目前只需要300人就足够了。”石鹤表示。
据介绍,2010年公司就开始在车间实施MES系统,当初还只是覆盖2到3个工艺节点,如今已经覆盖产品全生命周期7个节点。目前各车间已经实现MES生产互联,可做到生产过程实时调度管理,对生产设备运行状态指标实现实时监控、故障自动报警和诊断分析,生产任务指挥调度实现可视化,产品生产计划、生产过程所需的物流均可在系统中实现实时安排和调整。
通过覆盖产品全生命周期,公司还可以做到产品质量可追溯。同时,在关键工序采用智能化质量检测设备,建立了产品质量数据库,产品关键质量指标、计量管理数据均可利用MES信息系统进行管理,产品质量合格率稳定在99%以上。
“通过智能车间改造,组件和电池车间自动化程度接近80%,极大提高了车间的生产效率。”石鹤表示。
下一步,对于电池车间,公司计划未来优先导入各机台自动上下料装置,同时会考虑导入车间自动化传输系统,实现机台与机台之间的传递互联,预计项目完成后,可在现有基础上节省人力40%以上,极大提高车间的生产效率。另外,对于组件车间,未来计划在全厂区范围内导入自动串焊机和全自动化流水线,同时导入自动包装系统,预计可在现有的基础上节省人力15%以上,在一定程度上进一步实现产品良率和效率的提升。
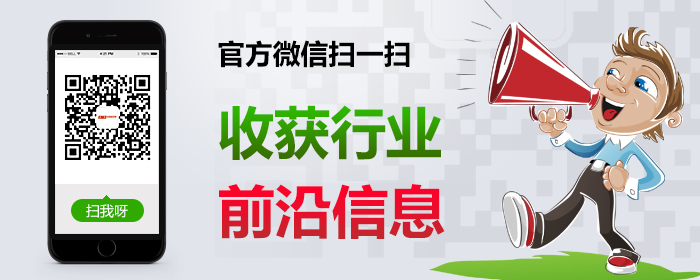
