LED封装*概述
LED封装技术大都是在分立器件封装技术基础上发展与演变而来的,但却有很大的特殊性。一般情况下,分立器件的管芯被密封在封装体内,封装的作用主要是保护管芯和完成电气互连。而LED封装则是完成输出电信号,保护管芯正常工作,输出:可见光的功能,既有电参数,又有光参数的设计及技术要求,无法简单地将分立器件的封装用于LED。
LED(发光二极管)封装是指发光芯片的封装。LED的封装不仅要求能够保护灯芯,而且还要能够透光,相比集成电路封装有较大不同。LED的封装不仅要求能够保护灯芯,而且还要能够透光。所以LED的封装对封装材料有特殊的要求。
LED 封装技术大都是在分立器件 封装 技术基础上发展与演变而来的,但却有很大的特殊性。一般情况下,分立器件的管芯被密封在封装体内,封装的作用主要是保护管芯和完成电气互连。而 LED封装 则是完成输出电信号,保护管芯正常工作,输出:可见光的功能,既有电参数,又有光参数的设计及技术要求,无法简单地将分立器件的封装用于LED。
LED 的封装的任务是将外引线连接到 LED 芯片的电极上,同时保护好 LED 芯片,并且起到提高光取出效率的作用。关键工序有装架、压 焊、封装。
LED封装*功能
1.机械保护以提高可靠性;
2.加强散热以降低芯片结温提高LED性能;
3.光学控制提高出光效率优化光束分布;
4.供电管理包括交流/直流转变以及电源控制。
LED封装*目的
半导体封装使诸如二极管、晶体管、IC等为了维护本身的气密性,并保护不受周围环境中湿度与温度的影响,以及防止电子组件受到机械振动、冲击产生破损而造成组件特性的变化。因此,封装的目的有下列几点:
(1)防止湿气等由外部侵入;
(2)以机械方式支持导线;
(3)有效地将内部产生的热排出;
(4)提供能够手持的形体。
以陶瓷、金属材料封装的半导体组件的气密性较佳,成本较高,适用于可*性要求较高的使用场合。以塑料封装的半导体组件的气密性较差,但是成本低,因此成为电视机、电话机、计算机、收音机等民用品的主流。
LED 封装*设备
由于 LED 封装要求较高,因此,无论是直插 LED 或贴片 LED,都必须使用具有高精度的固晶机,因为 LED 晶粒放入封装的位置 是否**,将直接影响整件封装器件发光效率。如果晶粒在反射杯内的位置有所偏差,光线不能被完全反射出来,直接影响 LED 的光亮度。但是,用一部具有先进的 PR System(预先图像辨识系统)固晶机,不论引线框架的品质差别,仍然可以将 LED 晶粒 **地焊接于预定位置上。
LED 封装*材料
半导体产品的封装大部分都采用环氧树脂。它具有的一般特性包括:成形性、耐热性、良好的机械强度及电器绝缘性。同时为防止对封装产品的特性劣化,树脂的热膨胀系数要小,水蒸气的透过性要小,不含对元件有影响的不纯物,引线脚(LEAD)的接着性要良好。单纯的一种树脂要能完全满足上述特性是很困难的,因此大多数树脂中均加入填充剂、偶合剂、硬化剂等而成为复合材料来使用。一般说来环氧树脂比其它树脂更具有优越的电气性、接着性及良好的低压成形流动性,并且价格便宜,因此成为*常用的半导体塑封材料。
LED 封装*特殊性
LED 封装技术大都是在分立器件封装技术基础上发展与演变而来的,但却有很大的特殊性。一般情况下,分立器 件的管芯被密封在封装体内,封装的作用主要是保护管芯和完成电气互连。而 LED 封装则是完成输出电信号,保护管 芯正常工作,输出:可见光的功能,既有电参数,又有光参数的设计及技术要求,无法简单地将分立器件的封装用于 LED。 LED 的核心发光部分是由 p 型和 n 型半导体构成的 pn 结管芯,当注入 pn 结的少数载流子与多数载流子复合时, 就会发出可见光,紫外光或近红外光。但 pn 结区发出的光子是非定向的,即向各个方向发射有相同的几率,因此,并 不是管芯产生的所有光都可以释放出来,这主要取决于半导体材料质量、管芯结构及几何形状、封装内部结构与包封 材料,应用要求提高 LED 的内、外部量子效率。常规 Φ5mm 型 LED 封装是将边长 0.25mm 的正方形管芯粘结或烧结 在引线架上,管芯的正极通过球形接触点与金丝,键合为内引线与一条管脚相连,负极通过反射杯和引线架的另一管 脚相连,然后其顶部用环氧树脂包封。反射杯的作用是收集管芯侧面、界面发出的光,向期望的方向角内发射。顶部 包封的环氧树脂做成一定形状,有这样几种作用:保护管芯等不受外界侵蚀;采用不同的形状和材料性质(掺或不掺散 色剂),起透镜或漫射透镜功能,控制光的发散角;管芯折射率与空气折射率相关太大,致使管芯内部的全反射临界角 很小,其有源层产生的光只有小部分被取出,大部分易在管芯内部经多次反射而被吸收,易发生全反射导致过多光损 失,选用相应折射率的环氧树脂作过渡,提高管芯的光出射效率。用作构成管壳的环氧树脂须具有耐湿性,绝缘性, 机械强度,对管芯发出光的折射率和透射率高。选择不同折射率的封装材料,封装几何形状对光子逸出效率的影响是 不同的,发光强度的角分布也与管芯结构、光输出方式、封装透镜所用材质和形状有关。若采用尖形树脂透镜,可使 光集中到 LED 的轴线方向,相应的视角较小;如果顶部的树脂透镜为圆形或平面型,其相应视角将增大。
一般情况下,LED 的发光波长随温度变化为 0.2-0.3nm/℃,光谱宽度随之增加,影响颜色鲜艳度。另外,当 正向电流流经 pn 结,发热性损耗使结区产生温升,在室温附近,温度每升高 1℃,LED 的发光强度会相应地减少 1% 左右,封装散热时保持色纯度与发光强度非常重要,以往多采用减少其驱动电流的办法,降低结温,多数 LED 的驱动 电流限制在 20mA 左右。 但是, LED 的光输出会随电流的增大而增加, 目前, 很多功率型 LED 的驱动电流可以达到 70mA、 100mA 甚至 1A 级,需要改进封装结构,全新的 LED 封装设计理念和低热阻封装结构及技术,改善热特性。例如,采用大面积芯片倒装结构,选用导热性能好的银胶,增大金属支架的表面积,焊料凸点的硅载体直接装在热沉上等方法。 此外,在应用设计中,PCB 线路板等的热设计、导热性能也十分重要。 进入 21 世纪后,LED 的高效化、超高亮度化、全色化不断发展**,红、橙 LED 光效已达到 100Im/W,绿 LED 为 501m/W,单只 LED 的光通量也达到数十 Im。LED 芯片和封装不再沿袭传统的设计理念与制造生产模式,在增加 芯片的光输出方面,研发不***于改变材料内杂质数量,晶格缺陷和位错来提高内部效率,同时,如何改善管芯及 封装内部结构,增强 LED 内部产生光子出射的几率,提高光效,解决散热,取光和热沉优化设计,改进光学性能,加 速表面贴装化 SMD 进程更是产业界研发的主流方向。
LED封装*封装工艺
封装工艺说明
1.芯片检验
镜检:材料表面是否有机械损伤及麻点麻坑(lockhill) 芯片尺寸及电极大小是否符合工艺要求 电极图案是否完整
2.扩片
由于 LED 芯片在划片后依然排列紧密间距很小(约 0.1mm),不利于后工序的操作。我们采用扩片机对黏结芯 片的膜进行扩张, LED 芯片的间距拉伸到约 0.6mm。 是 也可以采用手工扩张, 但很容易造成芯片掉落浪费等**问题。
3.点胶
在 LED 支架的相应位置点上银胶或绝缘胶。(对于 GaAs、SiC 导电衬底,具有背面电极的红光、黄光、黄绿芯 片,采用银胶。对于蓝宝石绝缘衬底的蓝光、绿光 LED 芯片,采用绝缘胶来固定芯片。) 工艺难点在于点胶量的控制,在胶体高度、点胶位置均有详细的工艺要求。 由于银胶和绝缘胶在贮存和使用均有严格的要求,银胶的醒料、搅拌、使用时间都是工艺上必须注意的事项。
4.备胶
和点胶相反,备胶是用备胶机先把银胶涂在 LED 背面电极上,然后把背部带银胶的 LED 安装在 LED 支架上。备 胶的效率远高于点胶,但不是所有产品均适用备胶工艺。
5.手工刺片
将扩张后 LED 芯片(备胶或未备胶)安置在刺片台的夹具上,LED 支架放在夹具底下,在显微镜下用针将 LED 芯片一个一个刺到相应的位置上。手工刺片和自动装架相比有一个好处,便于随时更换不同的芯片,适用于需要安装 多种芯片的产品.
6.自动装架
自动装架其实是结合了沾胶(点胶)和安装芯片两大步骤,先在 LED 支架上点上银胶(绝缘胶),然后用真空 吸嘴将 LED 芯片吸起移动位置,再安置在相应的支架位置上。 自动装架在工艺上主要要熟悉设备操作编程,同时对设备的沾胶及安装精度进行调整。在吸嘴的选用上尽量选用 胶木吸嘴,防止对 LED 芯片表面的损伤,特别是兰、绿色芯片必须用胶木的。因为钢嘴会划伤芯片表面的电流扩散层。
7.烧结
烧结的目的是使银胶固化,烧结要求对温度进行监控,防止批次性**。 银胶烧结的温度一般控制在 150℃,烧结时间 2 小时。根据实际情况可以调整到 170℃,1 小时。 绝缘胶一般 150℃,1 小时。 银胶烧结烘箱的必须按工艺要求隔 2 小时(或 1 小时)打开更换烧结的产品,中间不得随意打开。烧结烘箱不得再其 他用途,防止污染。
8.压焊
压焊的目的将电极引到 LED 芯片上,完成产品内外引线的连接工作。 LED 的压焊工艺有金丝球焊和铝丝压焊两种。右图是铝丝压焊的过程,先在 LED 芯片电极上压上**点,再将 铝丝拉到相应的支架上方,压上**点后扯断铝丝。金丝球焊过程则在压**点前先烧个球,其余过程类似。 压焊是 LED 封装技术中的关键环节,工艺上主要需要监控的是压焊金丝(铝丝)拱丝形状,焊点形状,拉力。 对压焊工艺的深入研究涉及到多方面的问题,如金(铝)丝材料、超声功率、压焊压力、劈刀(钢嘴)选用、劈刀(钢 嘴)运动轨迹等等。(下图是同等条件下,两种不同的劈刀压出的焊点微观照片,两者在微观结构上存在差别,从而 影响着产品质量。)我们在这里不再累述。
9.点胶封装
点胶封装 LED 的封装主要有点胶、灌封、模压三种。基本上工艺控制的难点是气泡、多缺料、黑点。设计上主要是对材料 的选型,选用结合良好的环氧和支架。(一般的 LED 无法通过气密性试验) 如右图所示的 TOP-LED 和 Side-LED 适 用点胶封装。手动点胶封装对操作水平要求很高(特别是白光 LED),主要难点是对点胶量的控制,因为环氧在使用 过程中会变稠。白光 LED 的点胶还存在荧光粉沉淀导致出光色差的问题。
10.灌胶封装
灌胶封装 Lamp-LED 的封装采用灌封的形式。灌封的过程是先在 LED 成型模腔内注入液态环氧,然后插入压焊好的 LED 支架, 放入烘箱让环氧固化后,将 LED 从模腔中脱出即成型。
11.模压封装
模压封装 将压焊好的 LED 支架放入模具中,将上下两副模具用液压机合模并抽真空,将固态环氧放入注胶道的入口加热用液压 顶杆压入模具胶道中,环氧顺着胶道进入各个 LED 成型槽中并固化。
12.固化与后固化
固化与后固化 固化是指封装环氧的固化,一般环氧固化条件在 135℃,1 小时。模压封装一般在 150℃,4 分钟。
13.后固化 后固化 后固化是为了让环氧充分固化,同时对 LED 进行热老化。后固化对于提高环氧与支架(PCB)的粘接强度非常 重要。一般条件为 120℃,4 小时。
14.切筋和划片
切筋和划片 由于 LED 在生产中是连在一起的(不是单个),Lamp 封装 LED 采用切筋切断 LED 支架的连筋。SMD-LED 则是在一 片 PCB 板上,需要划片机来完成分离工作。
15.测试
测试 LED 的光电参数、检验外形尺寸,同时根据客户要求对 LED 产品进行分选。
16.包装
将成品进行计数包装。超高亮 LED 需要防静电包装。
LED封装*分类
根据不同的应用场合、不同的外形尺寸、散热方案和发光效果。LED封装形式多种多样。目前,LED按封装形式分类主要有Lamp-LED、TOP-LED、Side-LED、SMD-LED、High-Power-LED、Flip Chip-LED等
1.Lamp-LED(垂直LED)
Lamp-LED早期出现的是直插LED,它的封装采用灌封的形式。灌封的过程是先在LED成型模腔内注入液态环氧树脂,然后插入压焊好的LED支架,放入烘箱中让环氧树脂固化后,将LED从模腔中脱离出即成型。由于制造工艺相对简单、成本低,有着较高的市场占有率。
2.SMD-LED(表面贴装LED)
贴片LED是贴于线路板表面的,适合SMT加工,可回流焊,很好地解决了亮度、视角、平整度、可靠性、一致性等问题,采用了更轻的PCB板和反射层材料,改进后去掉了直插LED较重的碳钢材料引脚,使显示反射层需要填充的环氧树脂更少,目的是缩小尺寸,降低重量。这样,表面贴装LED可轻易地将产品重量减轻一半,*终使应用更加**。
3.Side-LED(侧发光LED)
目前,LED封装的另一个重点便侧面发光封装。如果想使用LED当LCD(液晶显示器)的背光光源,那么LED的侧面发光需与表面发光相同,才能使LCD背光发光均匀。虽然使用导线架的设计,也可以达到侧面发光的目的,但是散热效果不好。不过,Lumileds公司发明反射镜的设计,将表面发光的LED,利用反射镜原理来发成侧光,成功的将高功率LED应用在大尺寸LCD背光模组上。
4.TOP-LED(顶部发光LED)
顶部发光LED是比较常见的贴片式发光二极管。主要应用于多功能超薄手机和PDA中的背光和状态指示灯。
5.High-Power-LED(高功率LED)
为了获得高功率、高亮度的LED光源,厂商们在LED芯片及封装设计方面向大功率方向发展。目前,能承受数W功率的LED封装已出现。比如Norlux系列大功率LED的封装结构为六角形铝板作底座(使其不导电)的多芯片组合,底座直径31.75mm,发光区位于其中心部位,直径约(0.375×25.4)mm,可容纳40只LED管芯,铝板同时作为热沉。这种封装采用常规管芯高密度组合封装,发光效率高,热阻低,在大电流下有较高的光输出功率,也是一种有发展前景的LED固体光源。 可见,功率型LED的热特性直接影响到LED的工作温度、发光效率、发光波长、使用寿命等,因此,对功率型LED芯片的封装设计、制造技术显得更加重要。
6.Flip Chip-LED(覆晶LED)
LED覆晶封装结构是在PCB基本上制有复数个穿孔,该基板的一侧的每个穿孔处都设有两个不同区域且互为开路的导电材质,并且该导电材质是平铺于基板的表面上,有复数个未经封装的LED芯片放置于具有导电材质的一侧的每个穿孔处,单一LED芯片的正极与负极接点是利用锡球分别与基板表面上的导电材质连结,且于复数个LED芯片面向穿孔的一侧的表面皆点着有透明材质的封胶,该封胶是呈一半球体的形状位于各个穿孔处。属于倒装焊结构发光二极管。
LED封装*污染工序
本项目主要为小功率白光LED以及大功率白光LED封装产品的技术研发和生产。其主要污染物为点荧光粉、灌封、脱模、一切、包装等工序中产生的:荧光粉粉尘、废气(苯),噪声,切料,不合格产品等固体废弃物以及项目排放的办公生活污水、生活垃圾等。其中:
1.废气:本项目产生的废气主要为生产过程中点荧光粉、灌封、脱模、一切、包装等工序中产生的荧光粉粉尘、废气苯,系为无组织排放。
2.废水:本项目生产过程中无废水排放,仅为办公生活污水,年排放量约2520t/a。办公区生活污水经园区化粪池处理后,排入项目 市政污水管网,*终进入 污水处理厂集中处理,
3.固废:主要是生活垃圾、在生产过程中产生的少量切料、不合格产品以及模具、包装材料等,生活垃圾年排放量约21t/a,生产垃圾年排放量约150t/a。
4.噪声:本项目主要为LED封装产品的技术研发和生产,生产所需元器件和电路板均为外购,生产过程为人工安装无大型噪声设备。主要的噪声源为空压机、风机等,噪声值为70~80 dB(A)。
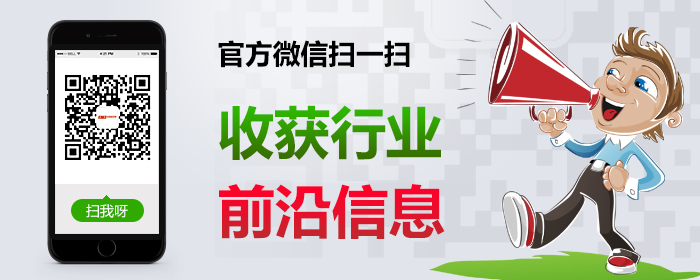